What is a Floor Screed?
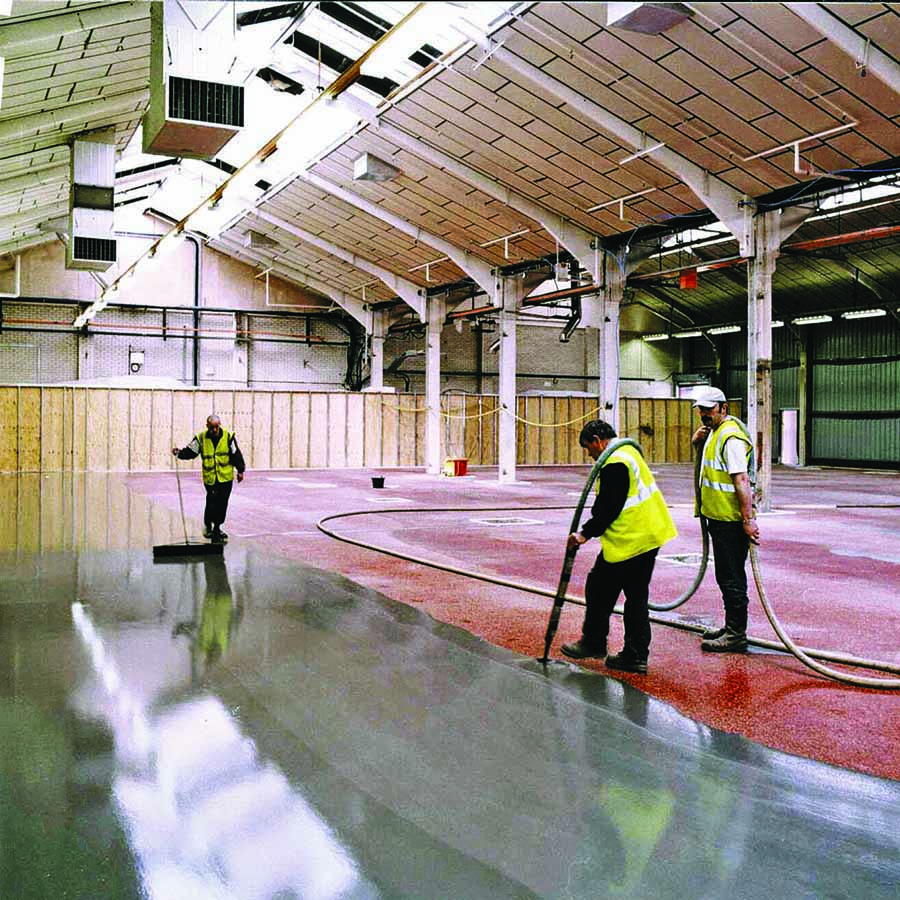
Floor screeds are applied over a concrete or asphalt base to provide a smooth and level surface for the final flooring system. Polycote have various types of floor screeds available, each designed to serve a specific purpose and with its unique set of benefits.
Understanding Floor Screed
Definition and Purpose
A floor screed is a mixture of cement, sand, and water that is poured or troweled onto a concrete or asphalt subfloor and is an essential component of any construction project. The floor screed provides a solid foundation with a hard wearing surface as well as ensuring the smooth surface needed for final flooring finishes.
The primary purpose of floor screed is to create a level and stable surface, which will not only support the final flooring system, but also provide additional benefits such as insulation and moisture resistance. A well-laid floor screed can help to improve the overall energy efficiency of a building by reducing heat loss through the floor. Additionally, it can help to prevent dampness and moisture from seeping into the building, which can cause structural damage over time.
Types of Floor Screed
There are several types of floor screed available in the market, each with its own unique set of properties and benefits. The most common types of floor screed include:
- Traditional cement sand screed
- Liquid screed
- Fast-drying screed
- Fiber-reinforced screed
- Polymer-modified screed
Traditional Cement Sand Screed
The most commonly used type of floor screed is the traditional cement sand screed. It is made up of a mixture of cement, sand, and water. The curing time of a tradition screeds are approximately 2-4 weeks to dry completely. However, this is length of time is strongly influence by three main factors; the thickness of the screed laid, the atmospheric temperature and humidity levels.
Traditional cement sand screed are cost-effectiveness and typically laid to a depth of 50mm to 75mm. However, they can easily be laid to a thickness of up to 100mm making it ideal for uneven or sloping floors as well as providing excellent thermal conductivity when used in the covering of underfloor heating systems.
Liquid Screed
Liquid screeds such as Polycote Easiscreed offer a huge advantage over traditional screed. They are made up of a liquid polymer binder mixed with cement and other additives to create a flowing mix that can be laid to a laser level finish with faster and more efficient results. It can be laid at any thickness from 2mm to 50mm in one pour and is therefore the ideal choice for smoothing out rough, worn, and uneven concrete.
Requiring no specialist labour or equipment, other than a mixing paddle (fixed to a standard drill), a spiked roller to disperse any air bubbles within the mix and a pin-leveller to ensure the screed is laid to a consistent thickness, the mixed product can be poured onto the existing surface whereby it will flow out and create a smooth, non-dusting finish.
Commonly referred to as a ‘pumped screed’, Easiscreed can be laid at a rate of as much as 2000sq.m in one day and together with its extremely fast curing properties, which means it can accept forklift traffic after only 24 hours this ensures it remains the first choice for all industry and contractors alike.
Polycote Easiscreed also provides excellent thermal conductivity, making it ideal for use with underfloor heating systems.
Fast-Drying Screed
For projects with tight deadlines, fast-drying screed is the ideal choice. This type of screed contains additives that accelerate the drying process and can be ready for the final flooring system in as little as 24 hours.
Fast-drying screed is perfect for projects that require a quick turnaround time, such as commercial buildings or public spaces. It is also suitable for use with underfloor heating systems, providing excellent thermal conductivity and ensuring efficient heat distribution throughout the building.
Fibre-Reinforced Screed
Fibre-reinforced screed includes additional fibres such as glass or polypropylene, which help to improve the screed’s strength and durability. It is ideal for areas with heavy traffic or where the floor needs to withstand significant wear and tear.
Fibre-reinforced screed is a popular choice for industrial buildings, warehouses, and car parks. It can also be used in residential buildings, providing a durable and long-lasting finish that can withstand the demands of everyday life.
Polymer-Modified Screed
Polymer-modified screed includes synthetic resins, which enhance the mix’s properties such as strength, flexibility, and durability. It is suitable for use in areas with high humidity or where there is a risk of moisture damage.
Polymer-modified screed is perfect for use in bathrooms, kitchens, and other high-moisture areas. It provides a waterproof barrier that protects the underlying structure from moisture damage, ensuring a long-lasting and reliable finish.
In conclusion, choosing the right type of floor screed is critical to ensure a reliable and durable finish that meets your specific project requirements. Whether you opt for traditional cement sand screed, liquid screed, fast-drying screed, fibre-reinforced screed, or polymer-modified screed, each type has its unique set of properties and benefits that can help you achieve the perfect finish for your building.
Benefits of Using Floor Screed
When it comes to flooring, the importance of a level and flat surface cannot be overstated. A perfectly level floor is not only visually appealing, but it also makes the installation of the final flooring system much easier.
Improved Leveling and Flatness
The primary benefit of using floor screed is that it helps to create a perfectly level and flat surface which is essential for many applications, from the installation of machinery and equipment through to the installation of complete racking systems. In warehouses and factories, a level floor is crucial, not only for the safe movement of heavy machinery and equipment, but also for the safety of personally by reducing slip and trip hazards.
Enhanced Thermal and Acoustic Insulation
Depending on the type of floor screed being used, it can also provide additional benefits such as thermal and acoustic insulation. This means that the final flooring system will be more energy-efficient, as it will retain heat better, and also be quieter, thanks to the sound-absorbing properties of the screed.
Thermal insulation is particularly important in colder climates, where it can help to reduce heating costs and improve energy efficiency. Acoustic insulation, on the other hand, is essential in environments where noise levels need to be controlled, such as schools, hospitals, and offices.
Increased Load-Bearing Capacity
Another significant advantage of using floor screed is that it can increase the load-bearing capacity of the concrete subfloor. This means that it can support heavier loads, which is especially important for commercial and industrial applications.
For example, in warehouses and factories, heavy machinery and equipment are often used, and a strong and sturdy floor is necessary to support their weight. Similarly, in car parks and garages, the floor must be able to withstand the weight of multiple vehicles.
Moisture Control and Damp Resistance
Finally, floor screed can also help to control moisture and prevent damp from seeping through the concrete subfloor. This is achieved by adding special additives such as Polycote Bondex to the mix that make it more resistant to water.
Moisture and damp can cause significant damage to buildings, and it is essential to take preventative measures to avoid any issues. By using floor screed, you can ensure that your flooring system is protected from moisture and damp, making it more durable and long-lasting.
Key considerations to ensure the right screed for your project
When selecting the right floor screed for your project, here are some important points for your consideration:
The amount of downtime that you can allow for the chosen screed to cure.
Whether the existing surface/screed needs to be removed
Any other considerations / influencing factors such as rising damp or surface contamination, such as oil, etc that could affect the adhesion of the new screed.
The thickness of screed required.
The type and amount of traffic / wear and tear that the screed will be subjected to.
The type of final flooring system to installed over the screed, whether if be paint, vinyl, carpet, wood, etc.
The level of insulation required.
These are just a few of the main considerations for your help. However, Polycote are just a phone call away. Ring us now and our trained advisors (who are mostly ex contractors with years of practical experience) can quickly and easily help guide you to the RIGHT type of floor screed for YOUR needs and ensure it is installed to the highest standards.
Related Articles
How to Screed a Floor Using Sand Cement Screed.
Polycote UK would like to take the opportunity to thank you for taking an interest in these product and application articles and hope they have been some help to you.
We would of course be pleased to answer any specific questions should you wish to contact us directly on 01234 846400 or email: help@polycote.com